Best Practices for Installing Commercial Electrical Systems in Brisbane
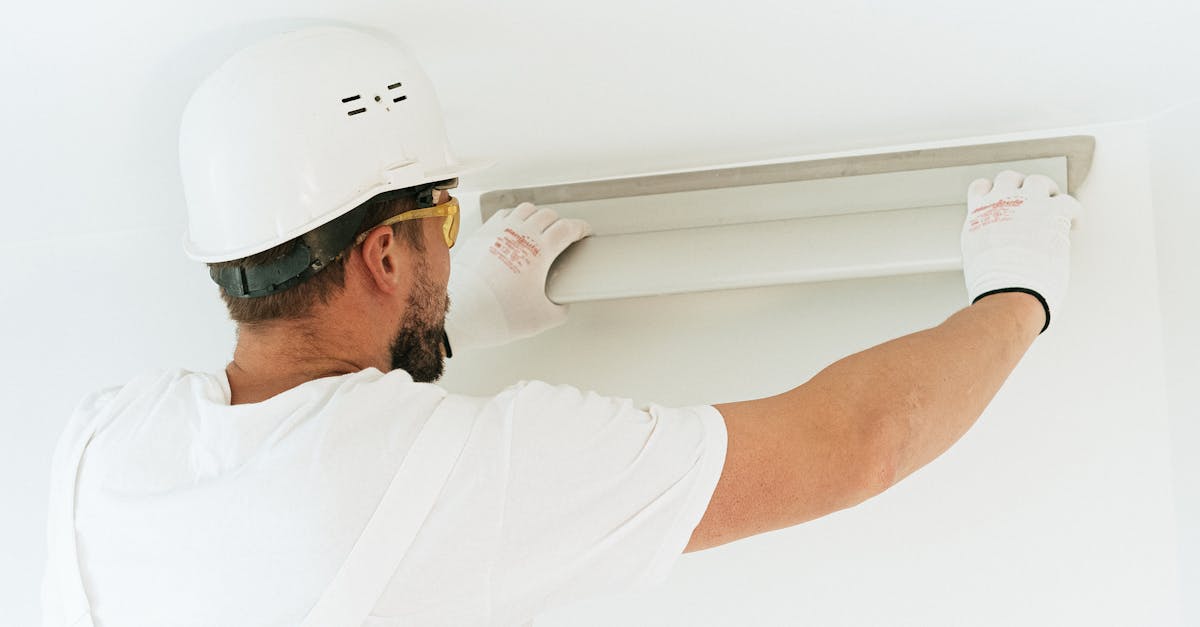
Table Of Contents
Implementing Safety Measures
When installing commercial electrical systems, prioritising safety is essential to protect both workers and property. Adequate training and certification for all personnel involved in the installation process ensure that they are knowledgeable about potential hazards and the regulations governing electrical work. This preparation helps create a safety-conscious environment, where team members understand the importance of risk assessments and the correct use of personal protective equipment.
Implementing effective safety measures also involves establishing clear communication among team members. Regular safety briefings can keep everyone informed about ongoing risks and methods to mitigate them. Furthermore, using appropriate signage and barriers around the worksite reduces the likelihood of accidents. Compliance with local regulations and standards adds an extra layer of security, creating a safer workspace while adhering to best practices within the industry.
Essential Safety Protocols for Installation
Prioritising safety during the installation of commercial electrical systems is crucial. Comprehensive risk assessments should be conducted before any work begins. This process identifies potential hazards and informs the development of mitigation strategies. Additionally, all personnel involved in the installation must receive appropriate training to ensure they understand safety protocols and emergency procedures.
Utilising the correct personal protective equipment (PPE) is non-negotiable. Each team member should wear relevant gear such as hard hats, gloves, and safety glasses to minimise risks. Regular safety briefings can reinforce the importance of protocol adherence. Implementing lockout/tagout procedures is vital for ensuring that electrical sources are properly shut off during installation, preventing accidental energisation and promoting a secure working environment.
Inspections and Testing
Thorough inspections and testing are indispensable in ensuring the reliability and safety of commercial electrical systems. These procedures help identify potential issues that could compromise performance. Experienced electricians should conduct these inspections, covering components such as wiring, circuit breakers, and connections. Regular assessments not only ensure compliance with safety standards but also extend the lifespan of the system.
Testing should include both functional and non-functional aspects. Functional testing verifies that each component operates as intended under various conditions. Non-functional testing evaluates parameters like temperature and load capacity. Documenting the results of these inspections and tests provides a vital record, supporting ongoing compliance and maintenance efforts. This approach helps prevent future problems and boosts overall safety within the commercial environment.
Ensuring System Functionality and Safety
Regular inspections and testing are vital to the reliability of any commercial electrical system. All components must be thoroughly examined following installation to ensure compliance with applicable safety standards. This includes testing circuit breakers, outlets, and wiring for proper functioning. Identifying issues early can prevent costly repairs and potential hazards down the line.
In addition to initial checks, ongoing maintenance plays a crucial role in ensuring safety. Routine testing should be scheduled to confirm that all equipment is operating correctly under load conditions. Keeping detailed records of inspections and maintenance activities assists in detecting trends over time. Proactive measures can significantly reduce the risk of electrical failures and boost overall system performance.
Maintenance Considerations
Regular maintenance is crucial for the longevity and efficiency of commercial electrical systems. Scheduling routine checks allows for the early identification of potential issues, thus preventing costly breakdowns or safety hazards. Inspecting components such as circuit breakers, wiring, and connections ensures that everything operates within the required specifications. Implementing a structured maintenance plan that includes periodic inspections will help in meeting compliance standards and improving the overall reliability of the system.
Training staff on basic maintenance practices enhances safety and operational efficiency. Ensuring that personnel understand the importance of reporting anomalies can lead to quicker responses to electrical issues. Moreover, keeping detailed records of maintenance activities aids in tracking the system's performance over time. This documentation can be invaluable for future upgrades or troubleshooting, ensuring a seamless operation of the electrical infrastructure.
Routine Checks for Optimal Performance
Regular inspections and maintenance are crucial for the longevity of commercial electrical systems. Technicians should schedule routine checks throughout the year to assess the condition of wiring, circuits, and equipment. This proactive approach helps identify potential issues before they escalate, ensuring any risks are mitigated promptly. Keeping documentation of these checks aids in tracking the system's performance over time, providing valuable insights into its operational efficiency.
Particular attention should be paid to connection points, circuit breakers, and fuses. This will help ensure that all components function as intended. Testing for wear and tear on cables, along with confirming that grounding systems are intact, also contributes to overall safety. Implementing these routine checks encourages optimal performance and minimizes the likelihood of unexpected downtime or costly repairs.
FAQS
What are the essential safety protocols for installing commercial electrical systems?
Essential safety protocols include conducting thorough risk assessments, using personal protective equipment (PPE), ensuring proper grounding and bonding, and following relevant Australian Standards and regulations.
How often should commercial electrical systems be inspected and tested?
Commercial electrical systems should be inspected and tested at least once a year, or more frequently if the system is subject to higher risks or changes in usage.
What maintenance practices should be followed for optimal performance of electrical systems?
Maintenance practices include conducting routine checks for any wear and tear, ensuring all connections are secure, cleaning electrical panels, and monitoring system performance regularly.
Are there specific regulations for commercial electrical installations in Brisbane?
Yes, commercial electrical installations in Brisbane must comply with the Australian Standards AS/NZS 3000:2018 and other relevant local regulations to ensure safety and functionality.
Can I perform my own maintenance on commercial electrical systems?
It is not recommended to perform your own maintenance unless you are a qualified electrician. Professional assistance ensures safety and adherence to regulations.
Related Links
Understanding the Role of Load Calculations in Electrical InstallationsInnovations in Electrical System Installation Techniques
The Impact of Building Layout on Electrical System Design
Common Mistakes to Avoid When Installing Electrical Systems
Compliance Considerations for New Electrical System Installations
Wiring Techniques for Optimising Commercial Electrical Installations
Essential Tools for Efficient Electrical System Installation in Brisbane