The Consequences of Ignoring Electrical Safety Standards
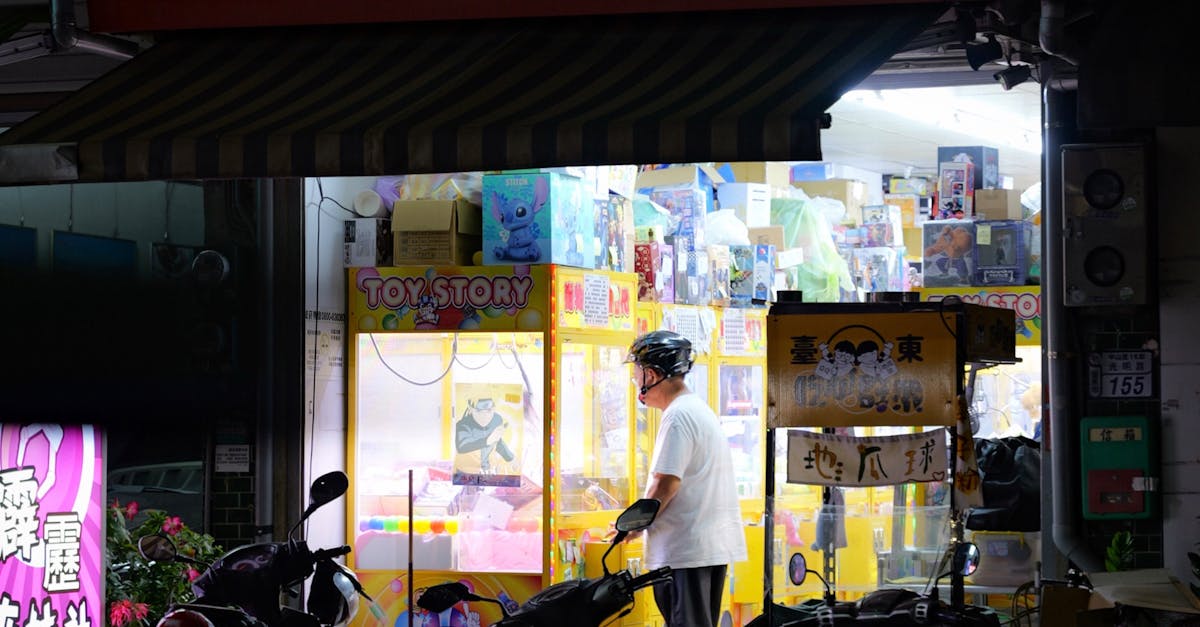
Table Of Contents
Financial Ramifications
Ignoring electrical safety standards can lead to significant financial setbacks for businesses. The cost of repairs associated with electrical malfunctions can quickly escalate, particularly if issues result in major damage to facilities or equipment. Many organisations may underestimate these expenses, believing that minor oversights will not lead to serious consequences. However, the reality of faulty wiring or outdated systems often leads to unforeseen costs that can disrupt operations and strain resources.
Medical bills stemming from workplace accidents caused by electrical hazards can further exacerbate financial woes. Injuries sustained by employees can lead to increased insurance premiums and potential litigation costs. Beyond the immediate financial implications, companies risk damage to their reputation and loss of productivity as they navigate the aftermath of incidents. Long-term financial stability can be threatened by a culture that prioritises short-term savings over adherence to safety standards.
Cost of Repairs and Medical Bills
Ignoring electrical safety standards can lead to significant financial burdens. When accidents occur due to negligence, the costs associated with repairs can escalate quickly. Damaged equipment may require replacements or extensive repairs, leading to downtime that affects productivity. Furthermore, facilities often face fines from regulatory bodies for non-compliance, compounding their financial losses.
Medical bills can soar in cases of electrical accidents. Injuries sustained by employees can lead to hospitalisation and lengthy recovery periods, resulting in lost wages for individuals and additional expenses for businesses. Worker's compensation claims may also rise, creating ongoing financial obligations. The cumulative effect of these costs highlights the importance of adhering to safety standards to mitigate potential expenses.
The Role of Training and Awareness
Effective training plays a critical role in promoting electrical safety in any organisation. Employees must understand the principles of safe electrical practices, including correct usage of equipment, recognition of potential hazards, and the importance of proper reporting procedures. Regular workshops and training sessions can help reinforce this knowledge and ensure that all staff are aware of the latest safety protocols. This proactive approach not only protects individuals but also fosters a culture of safety within the workplace.
Awareness campaigns can further solidify the importance of electrical safety among employees. Visual reminders, such as signage and informational pamphlets, serve as constant reinforcements of safe practices. Encouraging open discussions about safety concerns allows employees to voice their observations and experiences. This open dialogue contributes to a more engaged workforce and creates an environment where safety is prioritised. By consistently promoting safety awareness, organisations can reduce risks and encourage employees to take personal responsibility for their wellbeing and that of their colleagues.
Educating Employees on Safety Practices
Training employees on safety practices is essential for fostering a culture of electrical safety within an organisation. Workers equipped with adequate knowledge can identify potential hazards and respond effectively in emergencies. Workshops and practical demonstrations allow employees to gain hands-on experience while understanding the importance of compliance with safety standards.
Ongoing education ensures that employees remain updated on the latest safety protocols and technologies. Regular refresher courses can reinforce vital information while adapting to new regulations or advancements in equipment. This continuous learning approach not only reduces incidents but also encourages a proactive mindset regarding workplace safety.
Best Practices for Maintaining Electrical Safety
Regular inspections form a critical component of an effective electrical safety strategy. Inspections should be scheduled at appropriate intervals depending on the environment and usage patterns. Qualified personnel must conduct these reviews to ensure compliance with relevant safety standards. During inspections, any signs of wear, damage, or malfunction in electrical wiring and devices should be promptly addressed to prevent further risks. Maintaining comprehensive records of these inspections aids in tracking the facility's electrical health over time.
Routine maintenance routines are equally important in safeguarding electrical safety. This includes procedures such as tightening loose connections, cleaning dust from electrical appliances, and replacing outdated or damaged equipment. Ensuring that circuit breakers and fuses are functioning correctly contributes to overall system integrity. Adhering to a proactive maintenance schedule helps mitigate potential hazards, ultimately fostering a safer working environment.
Regular Inspections and Maintenance Routines
Establishing a routine for regular inspections is crucial in identifying potential hazards before they escalate into serious issues. Schedule assessments of electrical systems, wiring, and equipment to ensure they meet safety standards. Qualified professionals should conduct these inspections. They can provide insights into wear and tear that may not be immediately visible. Regular audits can preemptively address any deficiencies and help maintain compliance with relevant regulations.
Incorporating a maintenance routine also reinforces safety measures within the workplace. This can include checking circuit breakers, ensuring proper grounding, and verifying that all electrical equipment is functioning correctly. Documenting inspection results is vital for tracking compliance and addressing emerging risks. Regularly reviewing maintenance protocols contributes to a culture of safety, ensuring that the workplace remains secure for all employees.
FAQS
What are the financial consequences of ignoring electrical safety standards?
Ignoring electrical safety standards can lead to significant financial ramifications, including high repair costs, increased insurance premiums, and costly medical bills resulting from electrical accidents.
How can poor electrical safety standards affect employee safety?
Poor electrical safety standards can create hazardous working conditions, resulting in a higher risk of accidents, injuries, and even fatalities, thereby compromising employee safety in the workplace.
What are some effective training methods for educating employees on electrical safety practices?
Effective training methods include hands-on workshops, regular safety seminars, online training modules, and simulations that provide practical experience with safety protocols and emergency responses.
How often should electrical inspections and maintenance be performed?
Electrical inspections and maintenance should be performed regularly, ideally at least once a year, or more frequently depending on the specific equipment and environment to ensure ongoing safety compliance.
What are the best practices for maintaining electrical safety in the workplace?
Best practices for maintaining electrical safety include conducting regular inspections, ensuring proper training for employees, implementing safety protocols, and using high-quality equipment that meets relevant safety standards.
Related Links
Training Requirements for Electrical Safety in Commercial SettingsNew Developments in Electrical Safety Compliance in Brisbane
Common Mistakes in Electrical Safety Compliance
Safety Checklist for Electrical Installations in Brisbane
Evaluating the Effectiveness of Safety Protocols in Commercial Outlets
Best Practices for Conducting Electric Safety Assessments
The Role of AS/NZS Standards in Electrical Safety
Key Compliance Issues for Brisbane Electricians