Best Practices for Conducting Electrical Testing in Workplaces
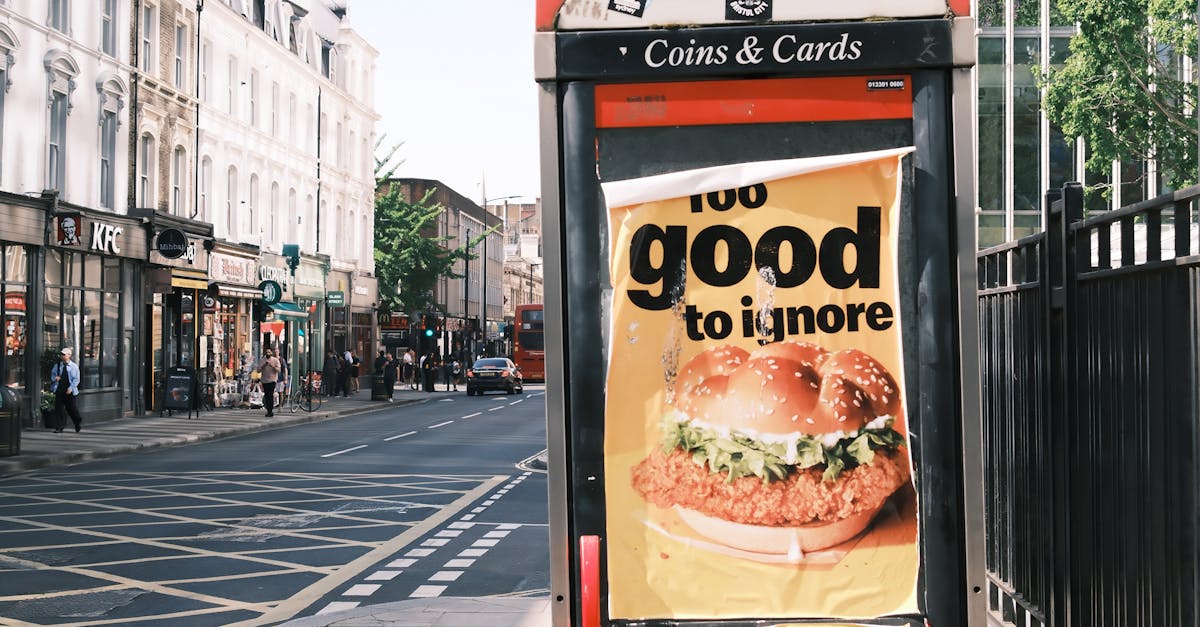
Table Of Contents
Training Personnel for Electrical Testing
Ensuring that personnel are properly trained in electrical testing is vital for maintaining workplace safety and compliance. Training programmes should encompass a comprehensive overview of electrical systems, relevant safety protocols, and the specific testing procedures applicable to the workplace and equipment. Emphasising hands-on training alongside theoretical knowledge is crucial, as practical experience allows workers to develop the necessary skills to perform tests accurately and efficiently.
In addition to initial training, ongoing education is essential to keep personnel informed about the latest industry standards and technological advancements. Regularly scheduled refresher courses can help reinforce skills and address any new safety practices that may arise. Involving employees in discussions about their experiences during testing can also highlight areas for improvement and enhance the overall competency of the team in managing electrical systems.
Skills and Knowledge Requirements
Personnel conducting electrical testing require a solid understanding of electrical principles and safety regulations. Familiarity with relevant standards and codes is crucial. Individuals should possess practical skills in using testing equipment effectively and interpreting test results accurately. This expertise ensures that personnel can identify potential hazards and mitigate risks in the workplace environment.
In addition to technical skills, effective communication and problem-solving abilities are essential. Teamwork plays a significant role in successful electrical testing, as collaboration often enhances safety measures and operational efficiency. Continuous training can help to keep staff updated on the latest advancements in testing technology and methodologies, contributing to a knowledgeable workforce equipped to handle various electrical challenges.
Documenting Electrical Test Results
Accurate record-keeping is crucial for maintaining compliance with safety regulations and standards. Test results should be documented systematically, capturing relevant details such as the type of test performed, the date, the equipment involved, and the names of personnel conducting the test. Having a well-organised record allows for easier reference during routine inspections or audits. It also provides historical data that can help in identifying trends or reoccurring issues.
In addition, thorough documentation aids in accountability within the workplace. Clear records make it easier to trace any faults back to their source, ensuring that necessary corrective actions are taken promptly. This transparency not only enhances safety but also supports effective management of maintenance schedules, leading to improved operational efficiency. Regular reviews of documented results can reveal insights that contribute to overall workplace safety and performance.
Importance of Accurate Record-Keeping
Accurate record-keeping during electrical testing is crucial for maintaining workplace safety and compliance. Detailed records provide a clear history of testing activities, which can be invaluable for audits, risk assessments, and regulatory inspections. Having comprehensive data readily available helps identify trends in electrical performance, guiding future maintenance and testing schedules. Properly documented results also facilitate informed decision-making regarding upgrades, replacements, or repairs.
In the event of electrical failures or incidents, precise records assist in tracing the origin of problems. This documentation allows technicians to review past test results, understanding the context of any faults. Furthermore, it serves as a legal safeguard, ensuring that the company can demonstrate adherence to safety standards and protocols. Keeping accurate records not only benefits the immediate operational context but also fosters a culture of accountability and diligence within the organisation.
Addressing Common Electrical Issues
Electrical systems may occasionally face common issues that can pose safety risks and operational inefficiencies. Regular inspections can help identify symptoms of wear, such as flickering lights or unusual sounds from equipment. These indicators often suggest that wiring may be outdated or damaged. Addressing these faults promptly is crucial to ensuring a safe working environment.
In many cases, it is necessary to engage qualified professionals to diagnose and repair electrical problems. Overloading circuits is a prevalent issue that can lead to equipment failure and potential hazards. Implementing routine maintenance checks can significantly reduce the likelihood of such faults. Recognising the early signs of electrical issues allows for proactive measures, ensuring safety and reliability within the workplace.
Identifying and Resolving Faults
Fault identification is crucial in maintaining a safe work environment. Regular electrical testing can help detect issues such as short circuits, overloaded circuits, and insulation failures. Technicians should be trained to recognise symptoms that might indicate underlying problems. Visual inspections, along with the use of testing equipment, are effective methods for diagnosing faults. Employing a systematic approach ensures that potential hazards are identified before they escalate into serious risks.
Once a fault has been identified, timely resolution is essential to minimise downtime and prevent further complications. Technicians must follow established protocols for repairs, which may involve isolating the affected circuit and implementing necessary fixes. It is also important for personnel to communicate findings to the relevant stakeholders, ensuring that everyone is aware of the situation and any additional safety measures required. Following proper resolution steps not only addresses immediate concerns but also helps in maintaining compliance with safety regulations.
FAQS
Why is training personnel important for electrical testing in the workplace?
Training personnel ensures they have the necessary skills and knowledge to conduct electrical tests safely and effectively, reducing the risk of accidents and ensuring compliance with safety regulations.
What specific skills and knowledge should personnel have for electrical testing?
Personnel should possess a strong understanding of electrical systems, safety protocols, testing equipment operation, and the ability to interpret test results accurately.
How should electrical test results be documented?
Electrical test results should be documented in a clear and organised manner, including details such as test dates, equipment used, results obtained, and any corrective actions taken.
Why is accurate record-keeping essential in electrical testing?
Accurate record-keeping is essential as it provides a reliable historical reference for maintenance, helps in compliance with regulations, and allows for effective tracking of any recurring issues.
What common electrical issues should be addressed during testing?
Common electrical issues to address include circuit overloads, faulty wiring, equipment malfunctions, and insulation failures, all of which can pose safety risks if not resolved promptly.
Related Links
The Role of Electrical Testing in Preventing Workplace HazardsStep-by-Step Guide to Electrical Tagging Procedures in Queensland
The Consequences of Neglecting Electrical Testing in Commercial Buildings
Training Requirements for Technicians in Electrical Testing and Tagging
Innovations in Electrical Testing Technologies for Compliance
How to Maintain Compliance with Testing and Tagging Regulations
Common Misconceptions About Electrical Tagging in Brisbane
Compliance Guidelines for Electrical Testing in Commercial Settings