Step-by-Step Guide to Electrical Tagging Procedures in Queensland
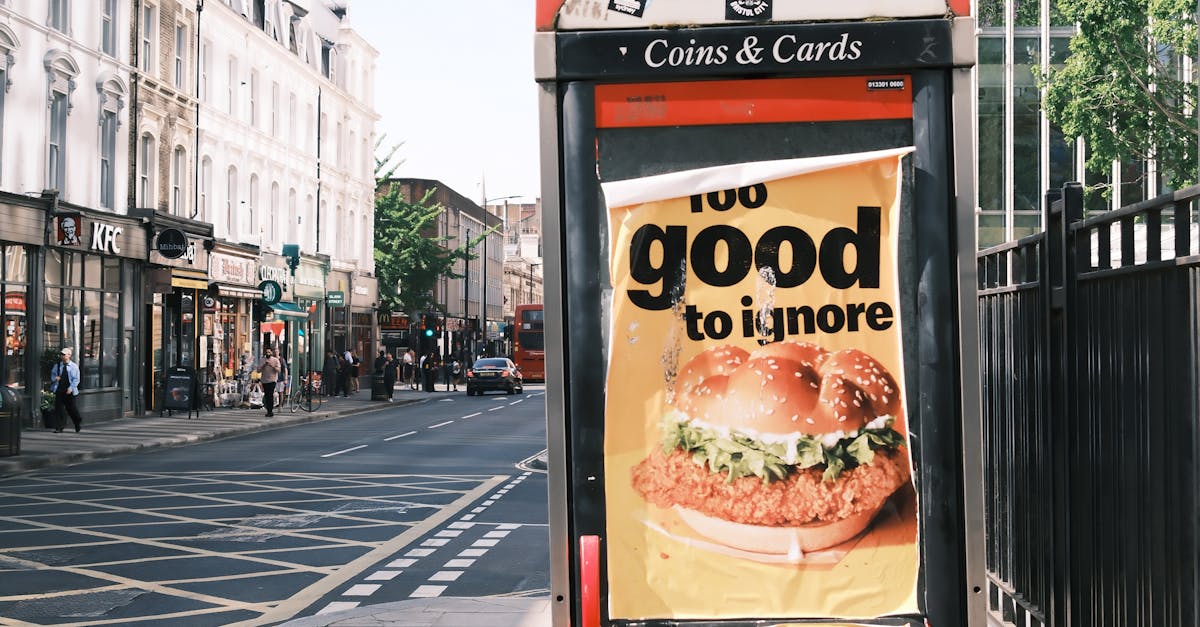
Table Of Contents
Step 2
Electrical testing is a crucial component of ensuring that equipment meets safety standards. Various types of tests are required for compliance, including insulation resistance testing, continuity testing, and earth leakage testing. Each test measures specific parameters that help in assessing the integrity and safety of electrical installations, enabling technicians to identify any potential hazards before they escalate into serious issues.
Additionally, the frequency of testing depends on the type of equipment and its operational environment. Regular testing not only helps in maintaining compliance with regulations but also extends the lifespan of electrical devices. Conducting these tests in a systematic manner ensures that any defects are documented and addressed promptly, fostering a safer workplace and minimising the risk of electrical failures.
Types of Tests Required for Compliance
Electrical compliance in Queensland mandates several tests to ensure safety and functionality. The most common types include Earth Continuity testing, Insulation Resistance testing, and Phase Rotation testing. Each test serves a specific purpose, verifying the integrity of the electrical system and its components. Earth Continuity testing checks the effectiveness of earthing conductors, ensuring that in the event of a fault, the electrical current has a low-resistance path to ground. Insulation Resistance testing measures the resistance between live conductors and earth, identifying potential hazards such as insulation breakdown.
Phase Rotation testing checks the sequence of the phases in three-phase systems. It ensures that motors and other equipment operate correctly, preventing potential damage from incorrect phase connections. These tests are crucial in maintaining compliance with the Australian Standards and ensuring that installations are safe for both users and technicians. Regular testing not only helps in meeting regulatory obligations but also enhances the longevity and reliability of electrical systems in various applications.
Step 3
Applying tags correctly is vital to ensure safety and compliance in any electrical environment. Double-check that the tag used is appropriate for the equipment and clearly indicates its status. It’s essential to ensure that tags are securely attached so they cannot be easily removed or damaged. Consider using tags made from durable materials designed to withstand conditions such as moisture, heat, and physical abrasion.
In addition to proper attachment, the visibility of tags plays a crucial role in effective communication. Tags should be placed in locations that are easily seen and understood by anyone interacting with the equipment. Using colour-coded tags can enhance instant recognition of the equipment's status, facilitating quick decision-making regarding safety and maintenance. Always adhere to local regulations and industry best practices when implementing tagging procedures to guarantee consistent and reliable safety measures.
Tagging Techniques and Best Practices
Proper application of tags requires attention to detail to ensure safety and compliance. It is essential to position tags securely so they are visible and easily identifiable. Tags should be affixed near the power source or connection point of the equipment being tested. This location helps in guiding personnel quickly to the equipment and understanding its status. Use durable materials that can withstand environmental factors such as moisture or heat, ensuring tags remain legible over time.
When applying tags, ensure that all relevant information is included. This typically covers the date of testing, the technician’s details, and the equipment’s current status. Consistency in tagging methods contributes to clarity and helps prevent misunderstandings regarding equipment safety. Additionally, it can be beneficial to colour-code tags based on the type of status, such as ‘in use,’ ‘out of service,’ or ‘tested and safe’. Such practices enhance communication among team members working with electrical equipment.
Step 4
Documentation is essential in the electrical tagging process. Maintaining accurate records ensures compliance with industry regulations and supports effective safety management. Each test performed, including the type of test, outcomes, and the person who conducted it, should be documented thoroughly. Ideally, these records are stored in a centralised system that is easily accessible to all staff involved in maintenance or safety inspections.
Attention must be given to the details in record-keeping. Any discrepancies or incomplete documents can lead to significant issues during audits or safety inspections. Regular reviews of documentation help identify any gaps in compliance, enabling proactive measures to be taken. This not only ensures adherence to the legal requirements but also fosters a culture of safety within the organisation.
Importance of Accurate Records in Tagging
Maintaining accurate records during the electrical tagging process is essential for safety and compliance. These records provide a comprehensive overview of the testing conducted, including specific details about the equipment, the tests performed, and the results obtained. An organised record-keeping system ensures that all relevant information is readily accessible for future reference, audits, and inspections. It can also play a vital role in demonstrating adherence to statutory regulations.
Moreover, thorough documentation helps in tracking the maintenance history of electrical equipment. This is particularly important for identifying patterns or recurrent issues that may arise over time. Accurate records support prompt decision-making regarding repairs or replacements, ultimately contributing to the overall safety of the workplace. By documenting everything meticulously, businesses not only fulfil legal obligations but also foster a culture of safety and accountability within their operations.
FAQS
What are the key steps involved in electrical tagging procedures in Queensland?
The key steps include performing electrical testing, applying tags properly, and ensuring proper documentation and record keeping.
What types of tests are required for compliance in Queensland?
The types of tests required for compliance may include insulation resistance testing, earth continuity testing, and functional testing, among others.
How should tags be applied to electrical equipment?
Tags should be applied securely and visibly, following the specific tagging techniques and best practices to ensure they remain legible and intact.
Why is accurate record keeping important in electrical tagging procedures?
Accurate record keeping is essential to maintain compliance with safety regulations, facilitate inspections, and ensure that all testing and tagging activities are properly documented.
Where can I find more information about electrical tagging regulations in Queensland?
More information can be found on the Queensland Government's official website or through relevant industry bodies that provide guidelines and resources for electrical safety compliance.
Related Links
Best Practices for Conducting Electrical Testing in WorkplacesCompliance Guidelines for Electrical Testing in Commercial Settings
The Consequences of Neglecting Electrical Testing in Commercial Buildings
Training Requirements for Technicians in Electrical Testing and Tagging
Innovations in Electrical Testing Technologies for Compliance
How to Maintain Compliance with Testing and Tagging Regulations
Common Misconceptions About Electrical Tagging in Brisbane
The Role of Electrical Testing in Preventing Workplace Hazards