Common Misconceptions About Electrical Tagging in Brisbane
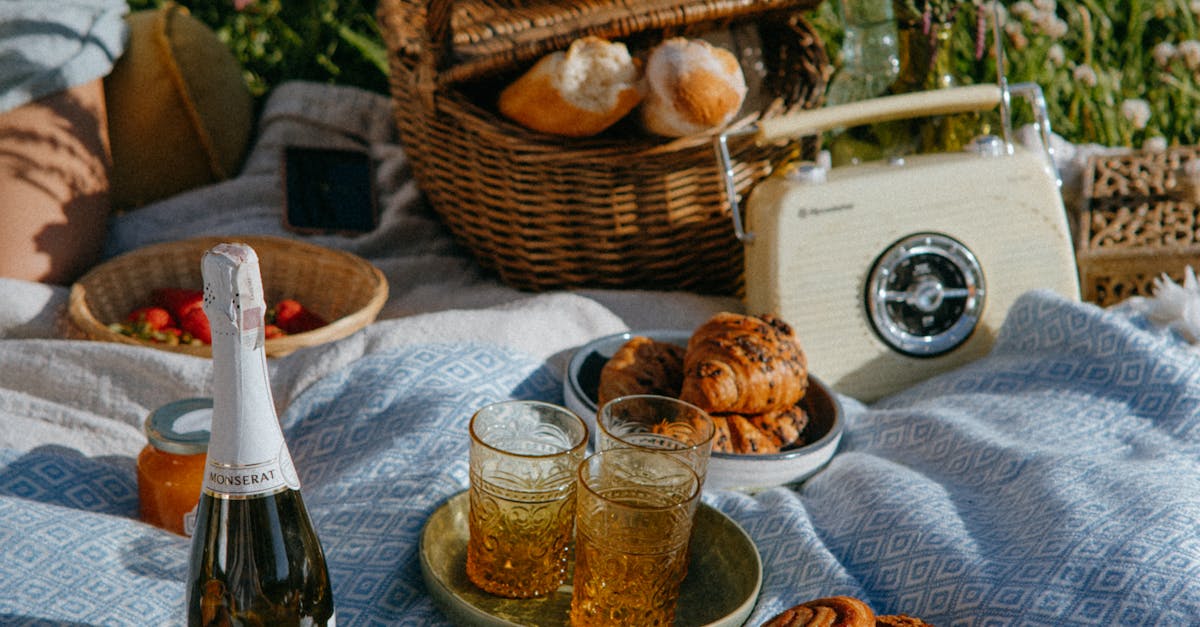
Table Of Contents
Misconception
Many individuals believe that electrical tagging is necessary only for large organisations due to the perception that they possess higher risks. This assumption overlooks the fact that small and medium enterprises also rely on electrical equipment to operate their businesses. Regardless of size, any establishment utilising electrical appliances must ensure compliance with safety standards to protect employees and customers.
There is a common belief that the tagging process is excessively time-consuming and complex. However, advancements in procedures have made it much more efficient than it once was. Qualified professionals can conduct tagging and testing with minimal disruption to business operations. This streamlined approach not only ensures safety but also facilitates compliance without causing significant downtime.
Applicability to Small Enterprises
Small enterprises often underestimate their need for electrical tagging, believing it only applies to larger corporations with extensive equipment. In reality, any business using electrical appliances must adhere to safety regulations. For small companies, complying with these regulations is equally crucial to protect employees and customers from potential hazards associated with faulty or untested equipment.
Engaging in regular electrical tagging can also benefit small businesses economically. Preventive measures reduce the risk of costly incidents and equipment failures, fostering a safer work environment. Additionally, demonstrating compliance with safety standards can enhance a small business's reputation. Clients and customers appreciate transparency and reliability, which can lead to increased trust and potentially more business opportunities.
Misconception
Many believe that electrical tagging is reserved solely for large businesses due to perceived compliance demands and significant safety protocols. This notion overlooks the fact that small enterprises also utilise electrical equipment. They have just as much responsibility to ensure the safety of their employees and customers. By adhering to tagging regulations, every business, regardless of size, can significantly mitigate risks associated with electrical hazards.
A further misconception lies in the assumption that the tagging process is burdensomely lengthy and overly complicated. In reality, professionals in the field have streamlined procedures designed to enhance efficiency. Companies can expect a straightforward process involving minimal disruption to daily operations. This efficiency supports adherence to safety standards while maintaining business productivity.
Importance of Regular Inspections
Regular inspections play a crucial role in maintaining the safety and compliance of electrical equipment. Over time, wear and tear can compromise the integrity of appliances, leading to potential hazards. Ensuring that tagging is renewed at appropriate intervals allows businesses to identify and rectify any issues before they escalate into serious problems. This proactive approach not only protects staff and customers but also ensures that operations continue without interruption.
Additionally, compliance with regulations is essential in avoiding penalties and maintaining a good reputation. Regular inspections provide an opportunity to assess the effectiveness of safety measures in place. They help to keep businesses informed about the condition of their equipment and highlight any necessary upgrades or improvements. Continuous monitoring ensures that everyone within the workplace adheres to safety standards, fostering a culture of accountability and care.
Misconception
Electrical tagging involves a systematic approach to ensuring that appliances and equipment are safe for use, which is often incorrectly perceived as being applicable solely to large businesses. This misunderstanding overlooks the fact that small enterprises, including home-based operations and independent contractors, benefit significantly from having their electrical equipment tagged. Compliance with safety regulations is essential for all businesses, regardless of size, and regular tagging helps mitigate risks associated with electrical hazards.
Another prevalent belief is that once the tagging process is completed, it does not require further attention. This notion fails to recognise the importance of ongoing inspections to account for wear and tear or changes in usage that may lead to potential safety issues. Regular checks and tagging updates ensure that equipment remains compliant with safety standards, reducing liability and promoting a safe working environment.
Streamlined Procedures for Efficiency
The tagging process has evolved significantly in recent years, with businesses implementing more efficient systems. Where previously the procedure could be time-consuming, advancements in technology have led to streamlined operations that minimise disruptions. This efficiency is particularly beneficial for businesses that need to maintain productivity while ensuring compliance with safety regulations.
Trained technicians now utilise faster methods for conducting inspections and affixing tags. By employing digital tools and automated workflows, the time spent on each unit can be drastically reduced. This ensures that companies can continue operations smoothly, giving them confidence in the safety of their electrical equipment without lengthy delays.
FAQS
What is electrical tagging?
Electrical tagging is a safety measure that involves inspecting, testing, and marking electrical equipment to ensure it meets safety standards and is safe to use.
Is electrical tagging only necessary for large businesses?
No, electrical tagging is essential for businesses of all sizes, including small enterprises. It helps ensure the safety of employees and customers, regardless of the company's scale.
How often should electrical tagging be done?
Electrical tagging should be conducted regularly, typically every six to twelve months, depending on the type of equipment and usage. Regular inspections help identify any potential safety issues before they become serious problems.
Is the electrical tagging process complicated?
While some may perceive the tagging process as complicated, it is typically streamlined and efficient when conducted by professionals. Certified technicians can complete the process quickly and effectively, minimising disruption to your business.
What are the consequences of not tagging electrical equipment?
Failing to tag electrical equipment can lead to severe safety hazards, including electrical fires or electrocution. Additionally, non-compliance with safety regulations can result in hefty fines and legal implications for businesses.
Related Links
How to Maintain Compliance with Testing and Tagging RegulationsThe Role of Electrical Testing in Preventing Workplace Hazards
The Consequences of Neglecting Electrical Testing in Commercial Buildings
Training Requirements for Technicians in Electrical Testing and Tagging
Innovations in Electrical Testing Technologies for Compliance
Best Practices for Conducting Electrical Testing in Workplaces
Step-by-Step Guide to Electrical Tagging Procedures in Queensland